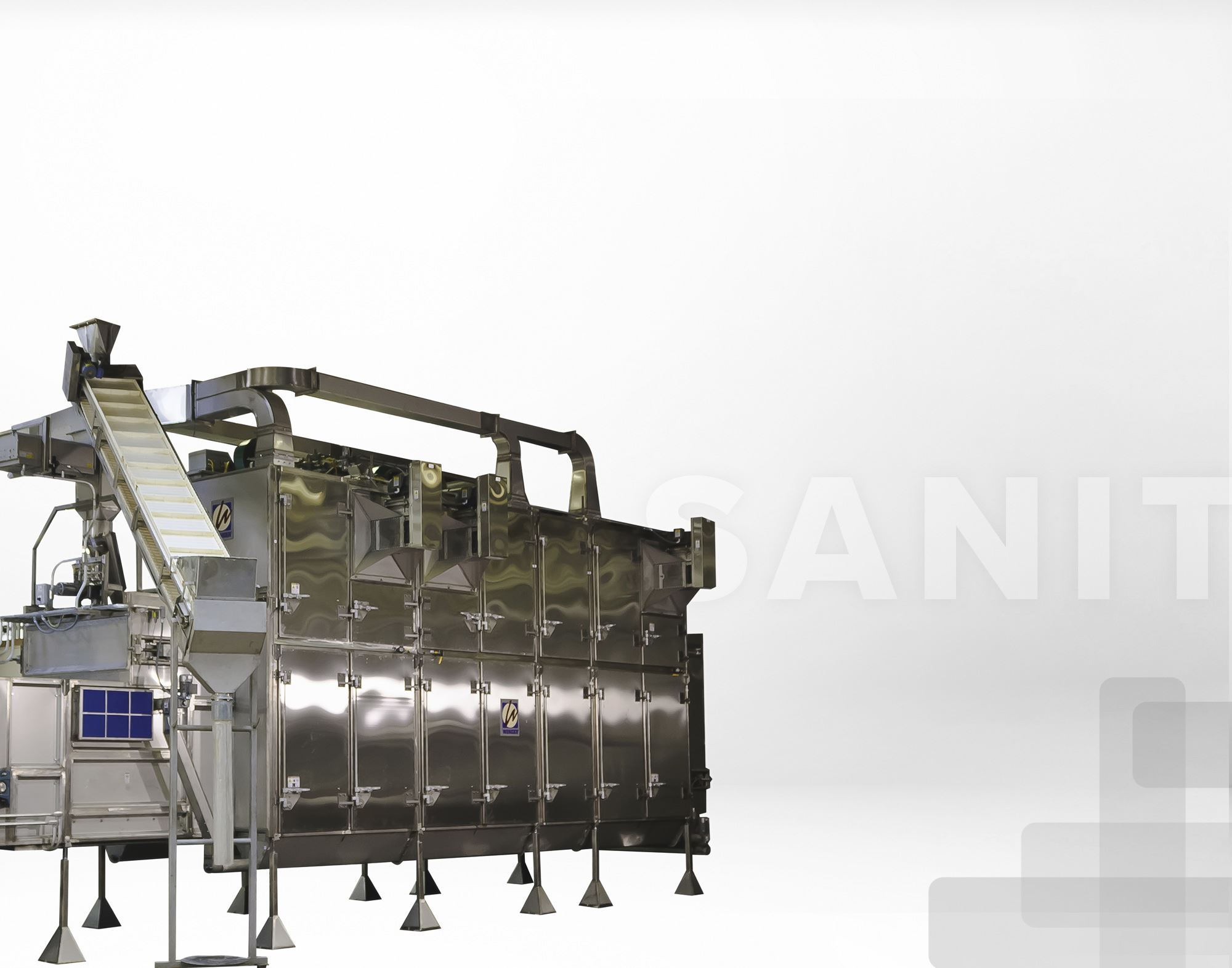
Enhanced Sanitary Dryer
Performance + Sanitation
The Enhanced Sanitary Dryer prevents cross-contamination while increasing efficiency due to decreased downtime for cleaning.
New Dryer Features
- Addition of insulated doors below process air fans
- Isolation floor separates wet incoming product from dry finish product
- Elimination of internal flat surfaces where practical, including no internal horizontal surfaces larger than 5 x 5 mm
- Minimum 30° slope on all internal ledges
- Improved geometry between mobile conveyor endplates and stationary flashing
- Modification of structural members
- Elimination of cracks and crevices that could collect fines and pathogens
- Increased access below upper and lower product conveyors
- Access panels at turnaround area of conveyors
- A direct-drive spout spreader that adjusts “on the fly”
Applications In
-
Food
Textured vegetable proteins, structured meat analogues, protein crisps, breadings, RTE cereals, snacks, hybrid products, and many more
-
Aquatic Feed
Floating, sinking, slow-sinking feeds, Recruiting Aquaculture Systems (RAS) feeds, and a wide variety of specialty feeds
-
Pet Food
Traditional kibble, semi-moist, high fresh meat inclusion, treats (long, short, filled, dental) - and flexibility for new products with numerous ingredient options
-
Industrial
With Wenger systems and know-how, you can create new products for a variety of industrial or consumer markets, or whatever idea you're thinking about.
-
Easier Cleaning
Quicker, easier cleaning begins with less accumulation of material. The Enhanced Sanitary Dryer has
eliminated the majority of surfaces where material can collect.
- Optimized conveyor end plates that provide more efficient airflow and less product spillage
- New chain and rail area slides that eliminate fines/kibble build-up and improve fines removal
- New conveyor side seals that prevent product spillage yet can be removed for cleaning
- Enhanced plenum fines augers that run the full length of the dryer for advanced fines removal
- Floor fines drags that continually clean dryer floors with 99% efficiency
- Polyester air filters on dryer and cooler makeup air openings filter room air as it enters the system
-
Advanced Control Options
Energy Control System
Minimize energy costs by 5% to 10% by optimizing the saturation of dryer process air. Energy control uses the internal process air to its full moisture removing potential before exhausting out of the dryer — optimizing energy efficiency.
Moisture & Energy Control System
Minimize moisture variation in the final product via data collected from the extruder APM. This system ignores moisture values input during unstable running conditions and can predict final moistures of less than =/-0.25 percent of a set point.
Technical Data
Widths |
---|
1,500 mm |
2,400 mm |
3,000 mm |
12-ton/hour model
Removes 17.7 sq. meters (190 sq. feet) of potential contamination points
450 liters (28,000 cu. inches) of fines and debris never accumulate
Talk to a Product Specialist
to discuss the feasibility, design and implementation for your project