Pet FoodINDUSTRY-LEADING PROCESSES
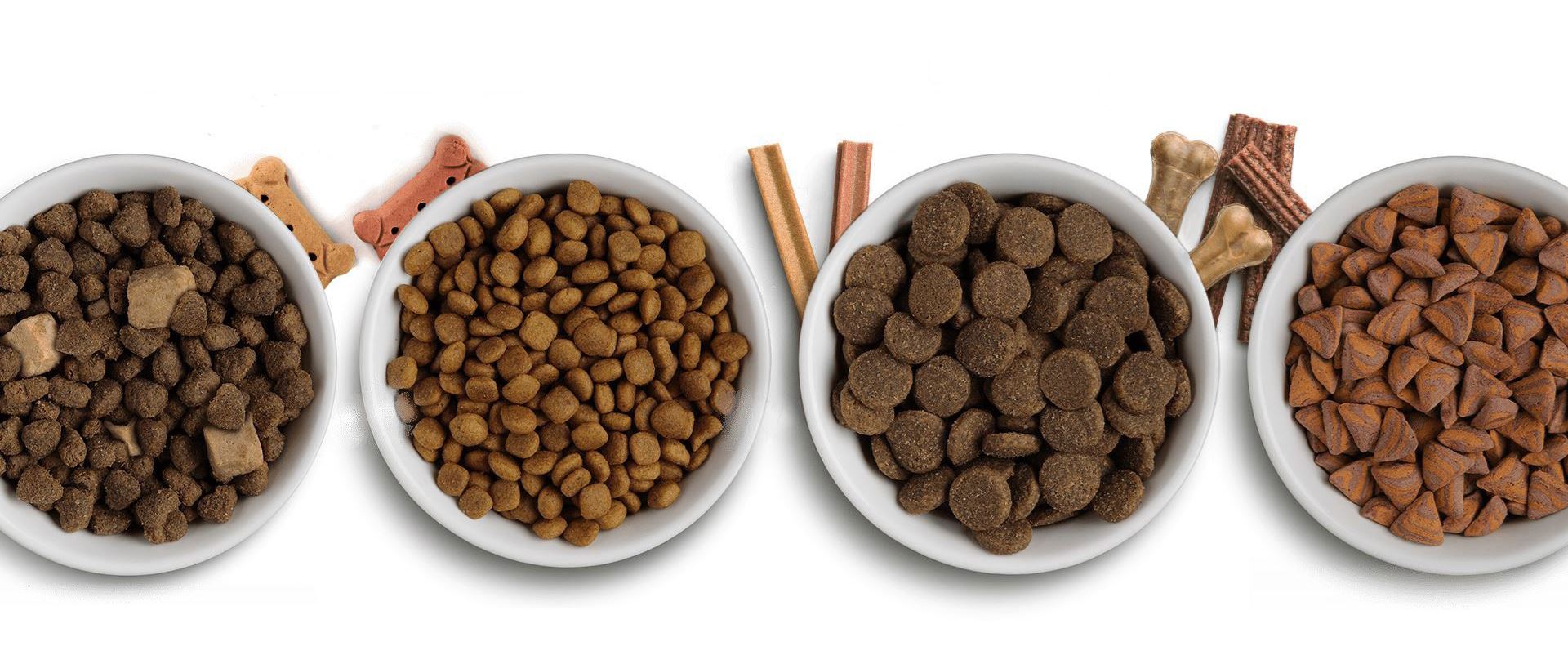
-
Greater Product Flexibility
Produce organic, functional and other on-trend products
Create unique textures and appetizing results
-
Unlimited Options
Soft bites, unique shapes, varied sizes and applications
Meet every demand of the specialty pet food market with our Petflex system
-
A Proven Leader
Continuous innovation and industry influence
Groundbreaking ingenuity recognized around the world
PetFlex Process
Centered around our Thermal Twin Extrusion technology, the PetFlex process boasts lower energy costs, less wear and lower environmental impact than other extrusion processes. It can be used for:
- Standard pet food
- High meat inclusions
- Baked treats
- Long goods
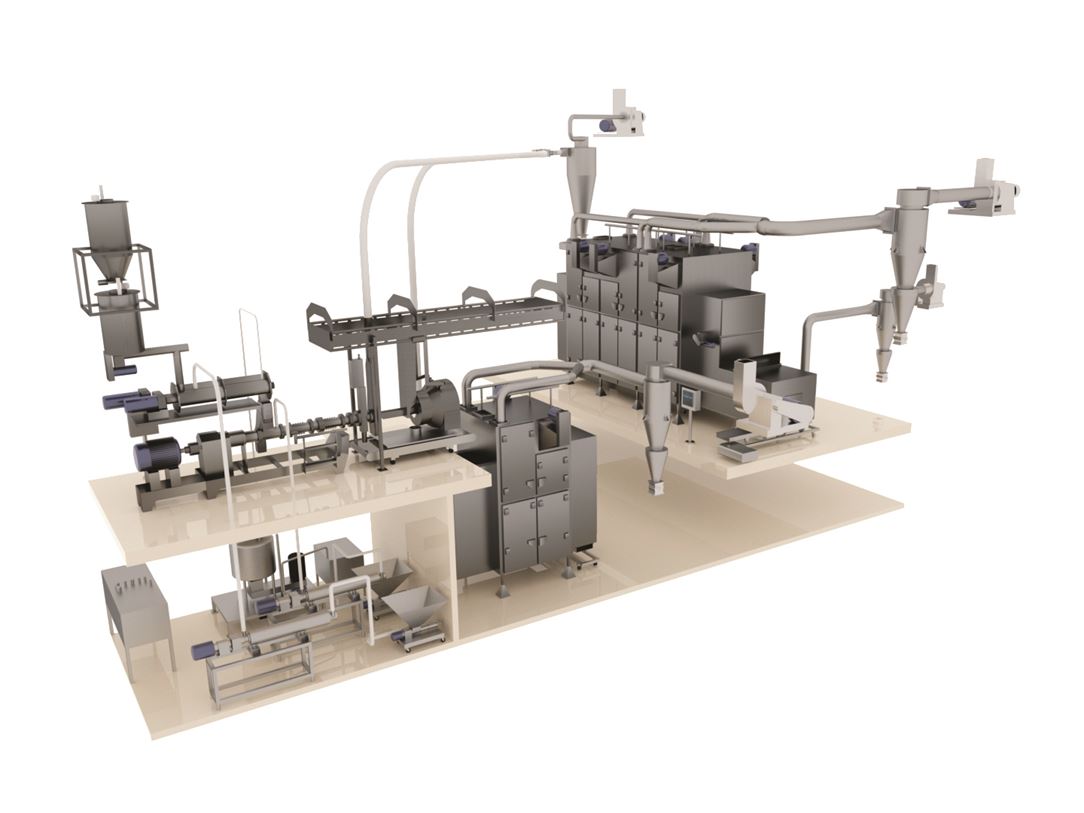
Extruders
Fresh Meat Pet Foods
Thermal Twin Extruders can produce:
-
STANDARD DOG FOOD
Standard dog food with moisture levels of 22% to 24%
-
Standard cat food
Standard cat food with moisture levels of 23% to 25%
-
HIGH AND ULTRA-HIGH FRESH MEAT PET FOODS
High and ultra-high fresh meat pet foods with up to 90% fresh meat and up to 40% moisture
-
BAKED PRODUCTS
Baked products with similar palatability results to other processes
Auto Density Control
Auto Density Control integrates three existing process components to provide automatic control of wet bulk density. It automatically measures product density and adjusts the process to maintain the desired density specifications.
- Programmed to collect and analyze a sample as often as 45 seconds
- Automatically adjusts the process to reach a new density setting in as little as 2 minutes
- Decouple personnel from the product for greater food safety
- Provide validation data for the process via the data display and recording capabilities of the system
Basic Components
Auto Density Control consists of three basic components:
- Source Technology’s sampling and bulk density measuring device (BDS)
- Wenger’s Automated Process Management (APM) system
- Wenger’s Back Pressure Valve (BPV) mounted on the end of the extruder to control specific mechanical energy input
Auto Density Control can be installed as part of a new system or retrofitted into a system that already has at least one of the basic components.
Request Info
to discuss the feasibility, design and implementation for your project
Research & Product Development
The Wenger Technical Center is an agrifood laboratory equipped with the latest in research and production scale extrusion and drying equipment. Let us assist you with:
- Product development
- Laboratory analysis
- Process evaluation
Project Feasibility, Design & Implementation
Count on our knowledge base and breadth of experience that is unsurpassed in extrusion processing and facilities construction.